A leader in advanced manufacturing
The MMRI is a state-of-the-art applied research and innovation centre that offers design and innovation services and training opportunities.
We provide the manufacturing industry with access to cutting-edge technology and equipment, as well a multi-disciplinary team with the expertise to solve real-world problems, overcome barriers and turn brilliant ideas into reality
-
21000
sq. ft.
-
20+
years experience in teaching, research and industrial activities
-
7
research labs
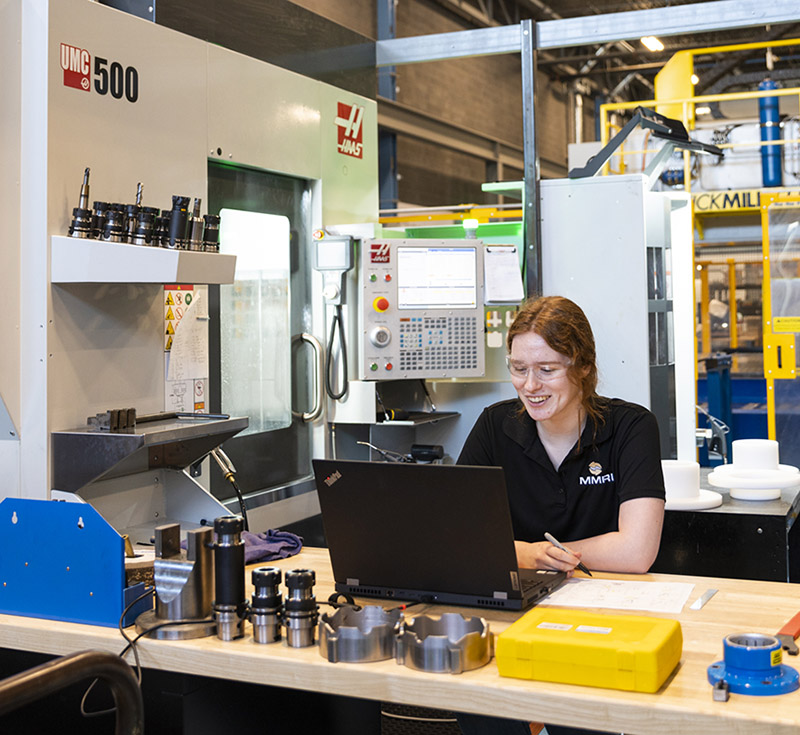
-
-
Take a virtual tour
-
Learn more about our machines
Gain training at the MMRI
We provide outstanding research and experiential learning opportunities, as well as problem-based educational programming.
Study with us
Are you interested in purusing a graduate-level degree in manufacturing engineering?
We provide training on the latest technologies and engaging applied research projects with industry partners.
Training program
Whether you are seeking employment, looking to increase your value in your company or just starting your career, the MMRI Industrial Training Program will give you the edge you need to stand out to employers.

Where to find us
230 Longwood Road South
Hamilton, Ontario, Canada
L8P 0A6
Follow our socials
Proud member of the OAMC: The Ontario Advanced Manufacturing Consortium
The partnership between the Advanced Manufacturing Consortium and our research facility is helping to create and build industry adoption of advanced manufacturing technologies. This partnership will create jobs and strengthen the province’s reputation as a leading manufacturing region. The partnership includes; McMaster University, University of Waterloo and Western University.