Collaborate with us
Industry collaboration is at the core of our research efforts. We can engage in short-term to multi-year technology transfer projects with our industry partners.
Government sponsored programs are available to facilitate University-Industry relationships through Ontario Centres for Excellence (OCE), National Sciences and Engineering Research Council (NSERC) and other programs. These groups offer grants to offset the cost of collaborative projects.
Contact us to improve quality, productivity and cost of your manufacturing processes
Technology transfer opportunities
We offer technology transfer opportunities for:
- Tooling selection
- Tool path development
- Process monitoring
- Process parameters

We combine our experience with state-of-the-art equipment to meet the sophisticated research and development needs of leading manufacturers.
The focus of this research group has been to develop intelligent solutions to issues faced by manufacturers in all steps of the machining process.
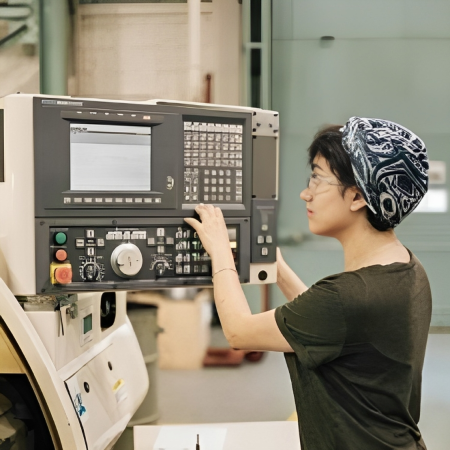
The MMRI can help you choose the correct tool for your process.
We use your material, process and tooling information to identify tool geometries, edge prepping and advanced tool coating which will significantly extend tool life and performance.
Our evaluation not only helps save tooling costs, it increases tool productivity and part quality. You will no longer have to “babysit” your processes thanks to the reduction of scrap rates.
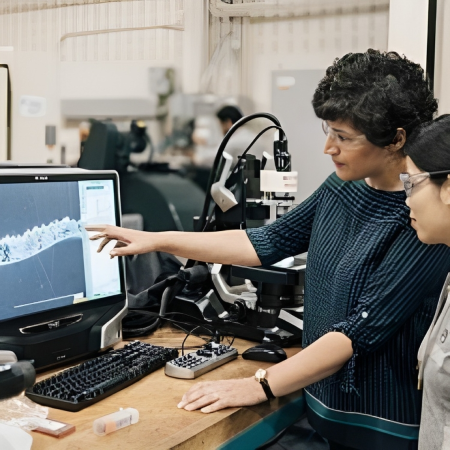
Improve your cycle times and push your machines to their full capability by utilizing the process simulation and optimization software: MACHpro.
MACHpro is the most advanced software of its kind in the market. With the ability to simulate your process in 5-axis and to automatically update your NC program, this software will help you to fully maximize your machines and tooling.
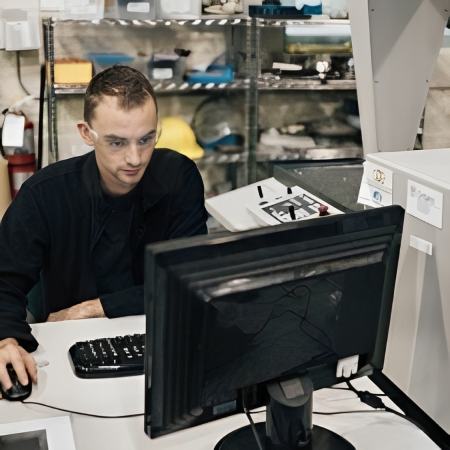
We can tune your process parameters, such as feeds and speeds, to optimize your production.
We use CUTPRO, a software developed by Manufacturing Automation Laboratories at the University of British Columbia, to intelligently identify optimal feeds. Our processing can improve your tool life, productivity, surface finishing and greatly impact your efficiency.
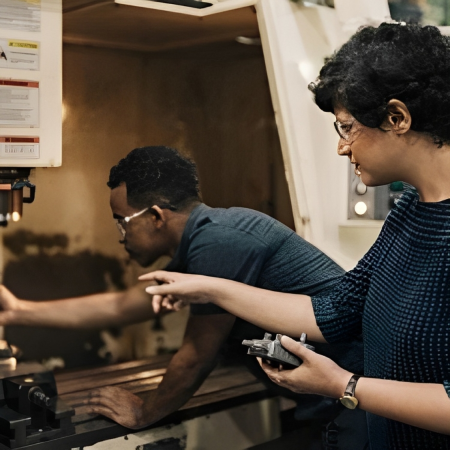
With use of our software, MMRI-Monitoring, you are able to track process production and production issues.
Our software is able to back your enhancement decision with detailed process data. It will alert you of production issues in real time, reduce variance and hold tighter tolerance on key dimensions.
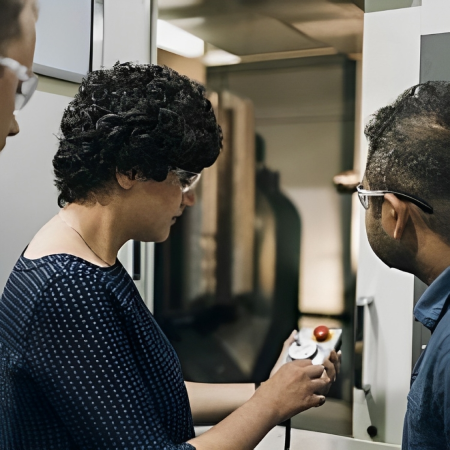
We have extensive experience in machining process optimization and improvement.
With our help we can improve part quality and productivity while lowering your costs. We have partnered with the Manufacturing Automation Laboratories at the University of British Columbia to be able to offer expertise and solutions to a wide range of machining challenges.
Partner success stories
The MMRI has found solutions to difficult real-world problems faced by Ontario manufacturers.
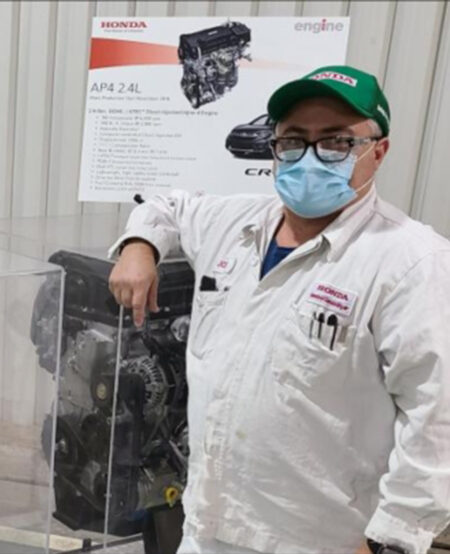
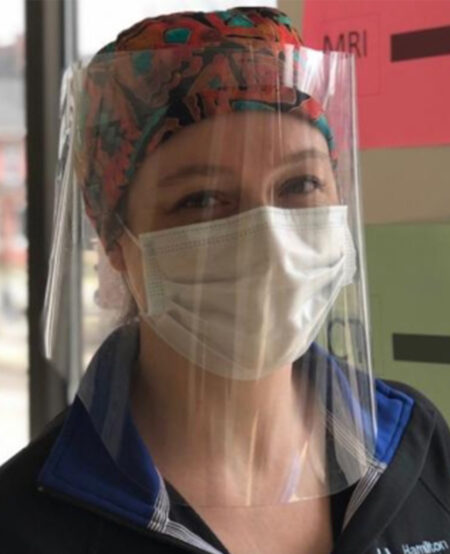
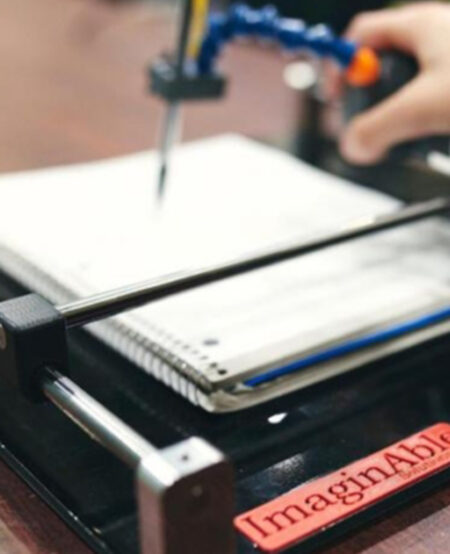
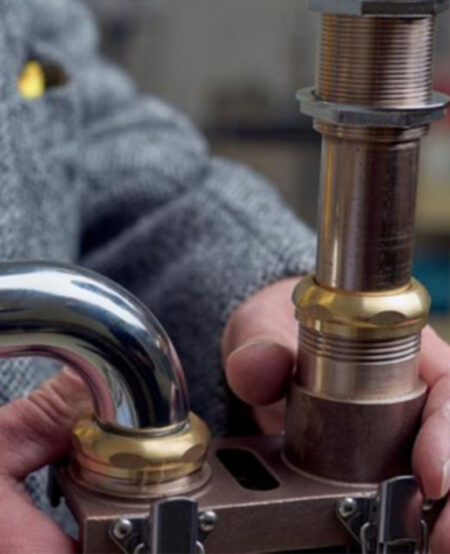
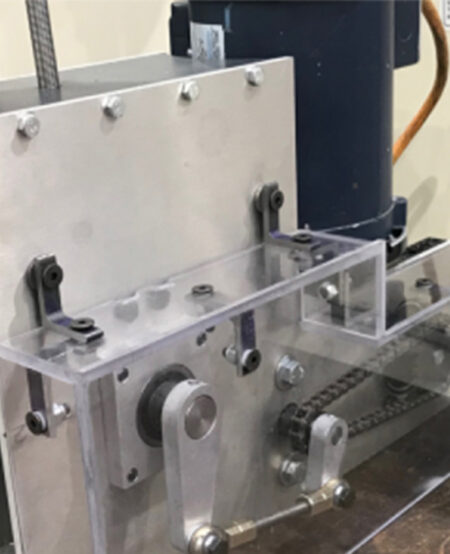
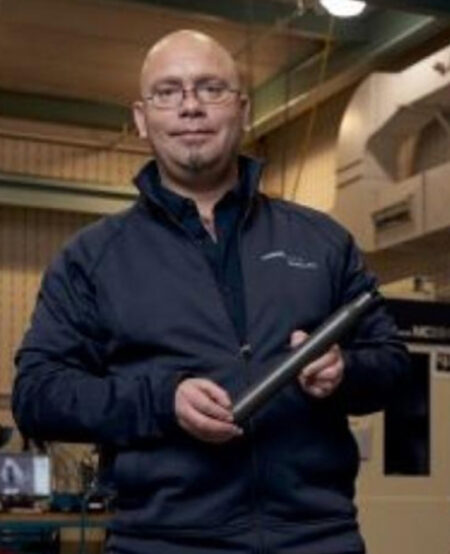
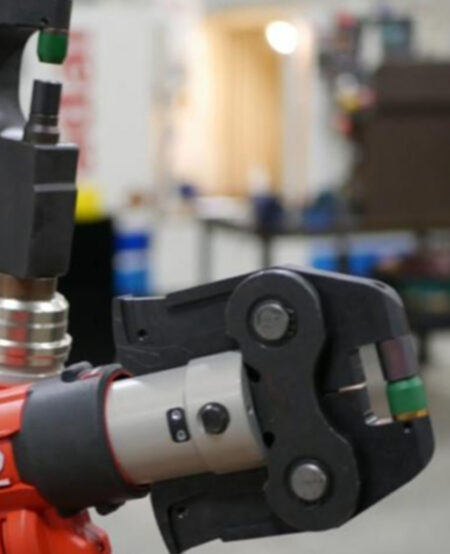