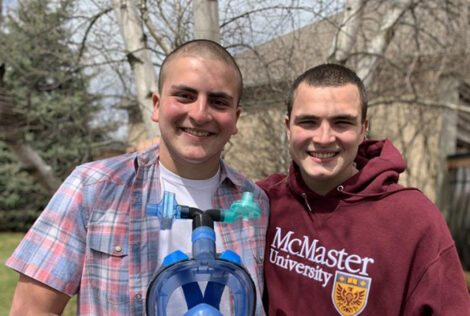
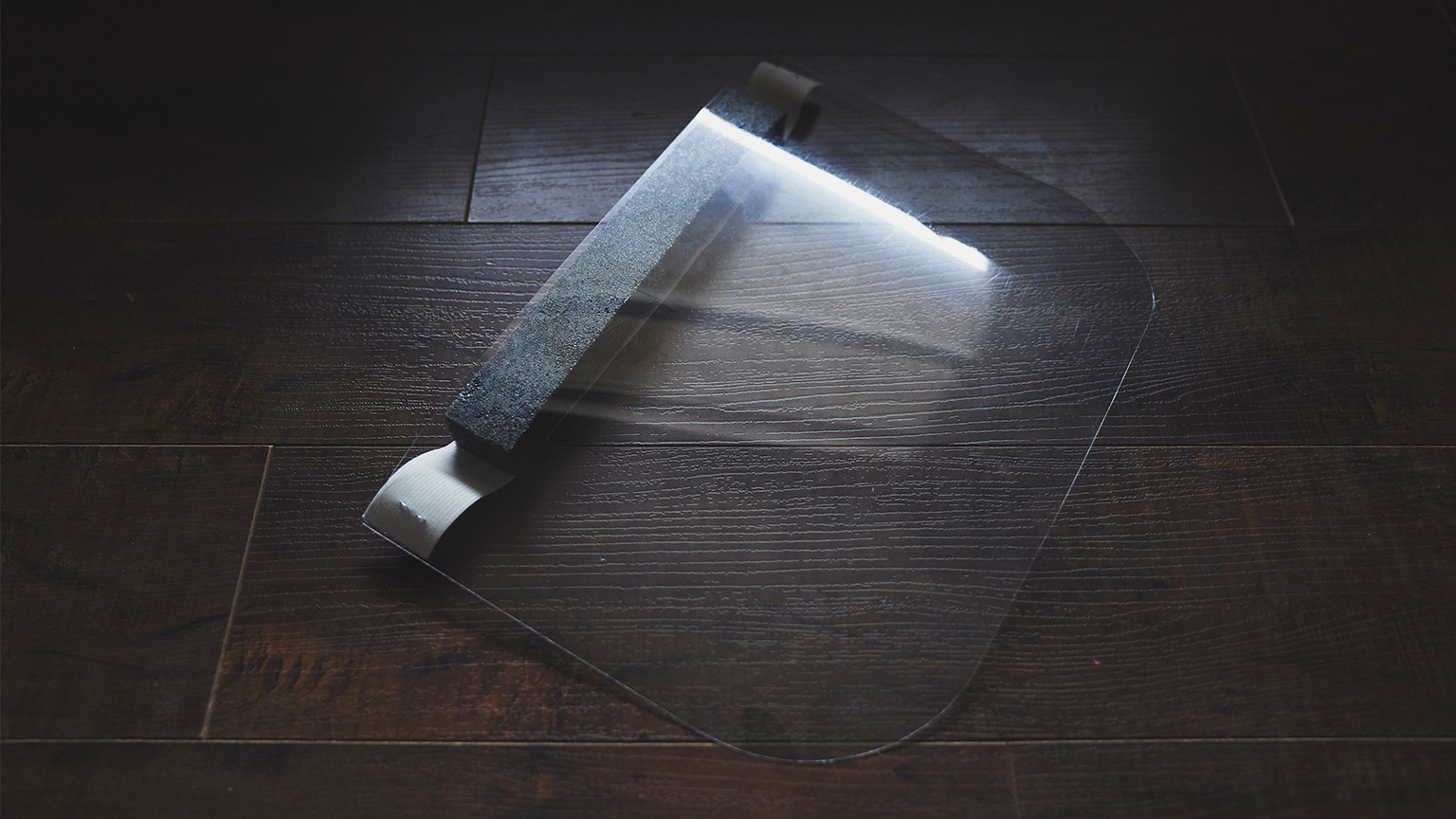
In the second part of the Mac Eng arms the frontlines series, we take a look at face shields.
Faculty, staff and students across McMaster Engineering have turned their focus on creating solutions to combat the shortage of personal protective equipment (PPE) for healthcare workers.
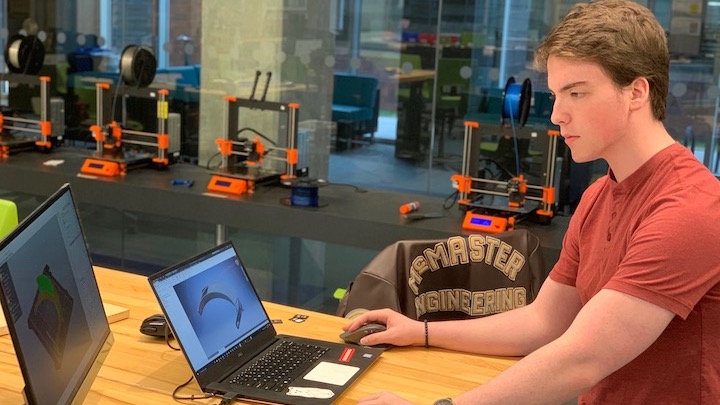
In addition to joining other faculties last week in a large donation of supplies to local hospitals, McMaster engineers are designing and testing face shields which can be made locally.
This comes amid a call from the federal government for homegrown solutions to increase “desperately needed” equipment in the fight against COVID-19.
Overseen and coordinated by Associate Dean of Research & External Relations John Preston and Dean Ishwar K. Puri, teams are working with manufacturing companies, government partners and local healthcare professionals with the goal of soon getting these prototypes to the frontlines.
“There are close to a hundred individuals across the faculty – faculty, staff members and students – involved in these activities, some remotely and others in labs across campus,” says Puri, calling the collective efforts “large and heroic.”
The efforts are being coordinated by the office of the Associate Dean of Research, connecting teams working on similar projects to move progress forward.
“There’s never been this kind of putting aside of egos and willingness to stretch outside of people’s comfort zones,” Preston told the CBC on Monday.
This story is part of a series looking at different ways MacEng is arming the frontlines. Here’s the first part on surgical and N95 masks. Below is the latest on the faculty’s face shield projects.
Supporting industry partners: Face shield production without 3D printers
What is it?
A team is looking into non-3D printed designs as an additional way to support local production of face shields.
Who is involved?
Simon Oomen-Hurst, program manager for the McMaster Manufacturing Research Institute (MMRI), is leading this project.
He’s working closely with Bryan Herechuk, manager of quality and value improvement at HHS, and Dr. Fox-Robinchaud.
They have partnered with Whitebird Manufacturing to repurpose the company’s existing equipment to produce face shields. A local food packaging company has also offered rolls of plastic to make into shields, and a cold call to Bra-Makers Supply led to a collaboration with a local company which is generously supplying elastic material for the face shield’s headband.
“It’s incredible how this has all played out. This all started with an email to Whitebird last Tuesday; they didn’t manufacture PPE but have equipment that could be re-purposed,” says Oomen-Hurst. “They were on board right away with their full support, and we started from zero.”
What is the status?
As of Wednesday, April 1 – about a week since the project began – the team has cleared “all major hurdles” and are ready to start production of more than 1,000 face shields a day.
“I think everyone is looking for ways to help fight COVID-19, and there is no way we could have done this so quickly without the overwhelming support we received,” says Oomen-Hurst.
The MMRI team works in close collaboration with Western University and the University of Waterloo as part of the Ontario Advanced Manufacturing Consortium. The three universities are currently sharing supplies of critically-needed materials to complete high-priority COVID-19 projects.
Engineering and Health Sciences team up, supported by iBioMed program
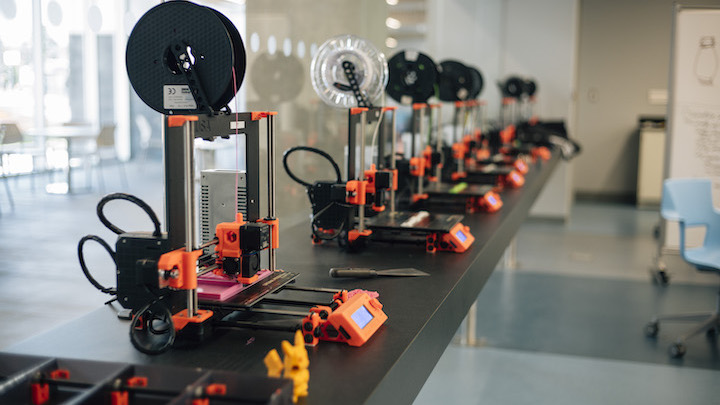
What is it?
McMaster teams are testing and deciding on the best face shield design to mass manufacture for healthcare workers. They’re repurposing existing spaces at McMaster with 3D printers to make face shields.
Who is involved?
This project is led by Tim Hillson, assistant clinical professor of surgery in the faculty of health sciences; Colin McDonald, director of Engineering 1; and Mike Noseworthy, co-director of the McMaster School of Biomedical Engineering. The team is repurposing existing spaces at McMaster with 3D printers to make face shields.
Dr. Alison Fox-Robichaud, a staff physician at Hamilton Health Sciences (HHS) and a professor in McMaster’s department of medicine, is vetting the face shield along with other emergency medicine physicians at HSS and St. Joseph’s Healthcare.
“Between our various lab spaces, we have a sizable fleet of 3D printers to produce several face shields each day, but what’s been remarkable is how quickly everyone has mobilized to move this project forward,” says McDonald.
This effort is largely supported by the Integrated Biomedical Engineering & Health Sciences program, also known as iBioMed, which is the first Canadian health sciences program to bridge together health, engineering science and entrepreneurship.
“We have students continually reaching out to us, asking how they can help. Their world is turned upside down right now, so it’s truly inspiring to see them thinking first and foremost of the well-being of our healthcare workers,” McDonald adds.
What is the status?
The face shields will be produced in the first-year Engineering EPIC Lab and the iBiomed Design Studio, where there are 25 printers in total. Discussions with local manufacturers on 3D printing are ongoing, with the goal to increase production capacity.
Our faculty get involved: Optimizing 3D Printing for Face Shields
What is it?
A group of engineers and physicians are investigating the best printing preferences for 3D printing face shields, such as infill percentage, number of solid layers and perimeter layers.
Who is involved?
This effort is led by Mohamed Ezzeldin, an assistant professor in the department of civil engineering.
He is collaborating with Dr. Mohamed Eltorki, an assistant clinical professor in the faculty of health sciences who works in pediatric emergency medicine.
“We do not want our frontline healthcare workers to be exhausted and worried over any lack of PPE. We’re gearing all our efforts to 3D-print robust head shields to ration respiratory protective devices, including N95 masks,” says Ezzeldin.
“Students, staff, and faculty members are working closely with local manufacturers to further the research and design for 3D printed PPE that comply with relevant standards.”
What is the status?
The group is updating the current 3D model files from a “face shield” to a “head shield” to achieve full head protection. The updated design files will be sent to several local hospitals for feedback.
Students take action: Baja Racing Team Face Shields
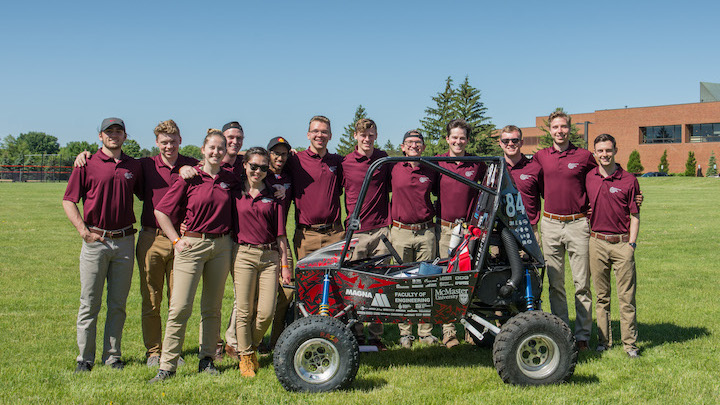
What is it?
Members of the McMaster Baja Racing team are working with 3D Printing Canada to join other faculty initiatives in printing face shields.
Who is involved?
Matt Lukas, McMaster Engineering Hatch Shop coordinator, initially reached out to the Baja Racing team to see if he could use the 3D printer in the Hatch Bay to print the face shields.
“After I reached out to my team to make them aware of the initiative, it became clear we had a few members with 3D printers sitting idle in their homes,” says Lacey Wice, who is this year’s team co-captain alongside Gabe Teichman.
She then contacted 3D Printing Canada, the main company behind this initiative in Hamilton, and with St. Joseph’s Hospital to get the files needed to print the face shields.
“We are simply trying to help from our homes,” Wice says.
What is the status?
The team hopes to start printing the face shields in the coming week.
Work with us! Find out how you or your organization can get involved