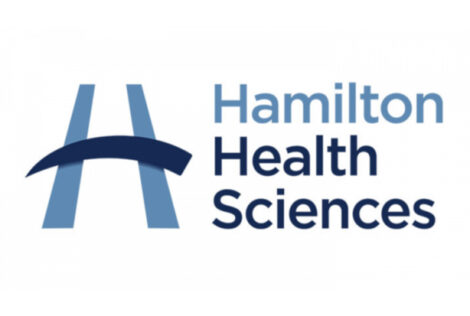
Global leaders in PPE
The Centre of Excellence in Protective Equipment and Materials assists research and development needs for Canadian companies, both existing and new, so that they can meet today’s needs for PPE Canada.
The centre also develops the next generation of personal protective equipment to become global leaders in the future.
Our story
The CEPEM was established in response to a call from Hamilton Health Sciences (HHS) to start local manufacturing of face masks and face shields due to the anticipated supply chain breakdown in March of 2020 caused by COVID-19.
In just over a month, the CEPEM team provided design, identified suitable materials and developed validation tests so that local manufacturers are now producing 20,000 face shields/day (Whitebird) and 20,000 masks/day (Niko apparel) to supply HHS.
In this process, the centre has also developed a testing facility that can assess various filtration materials for breathability (pressure drop), particulate filtration efficiency (PFE), bacterial filtration efficiency (BFE) and fit testing.
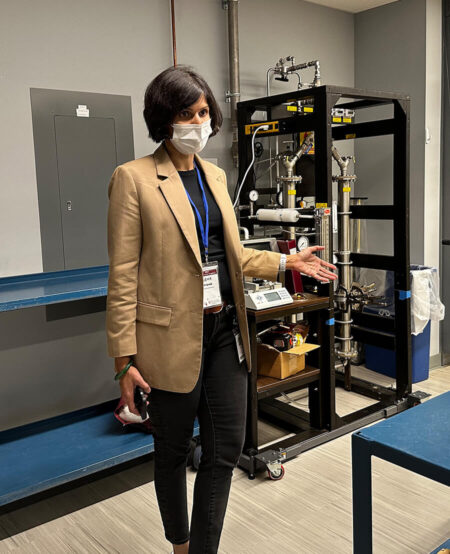