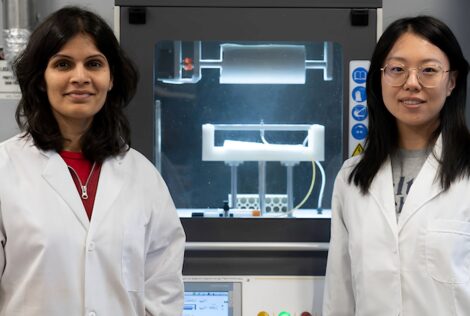
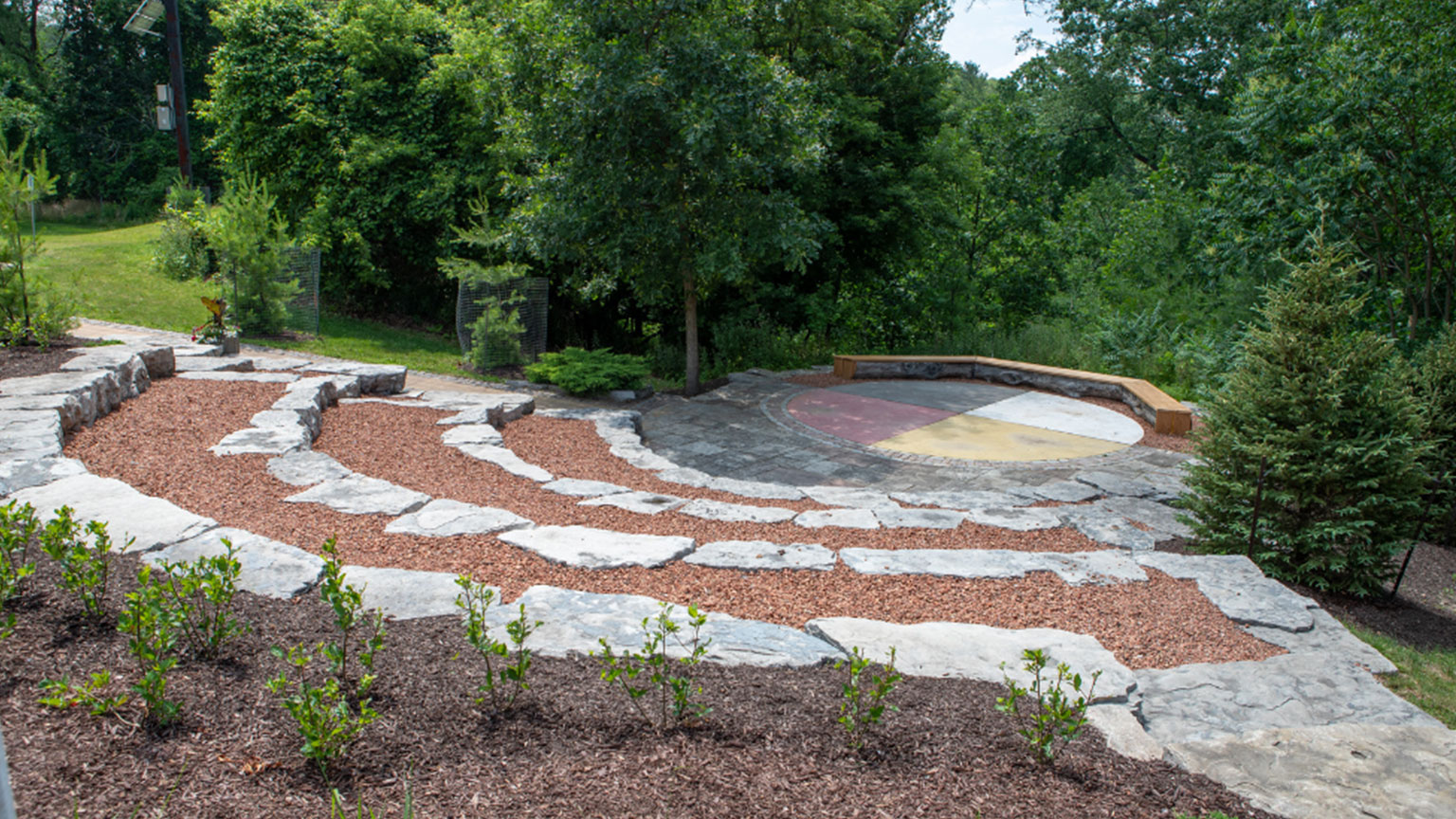
The W Booth School of Engineering Practice and Technology’s new Learning Factory is a world-class facility that simulates the factory of the future.
The facility, located in the basement of the Engineering Technology Building, introduces advanced manufacturing technologies to students and industry partners and provides the opportunity to work on hands-on projects to improve individual manufacturing processes.
“Our university has always been a key player in manufacturing research and education in the country,” says Mo Elbestawi, Director of the W Booth School of Engineering Practice and Technology at McMaster. “We chose to design a space based on our experience and the new knowledge we want to give to our students.”
The Learning Factory is arranged in several different manufacturing and post-processing stations. The manufacturing stations have equipment for metal additive manufacturing, CNC machine tooling, 3D printing, injection moulding, laser cutting and electronics. For post-processing there are stations for marking and tracing information about an item with a 2D bar code reader, assembly of mechanical and electronics components with two collaborative robots and a station for packaging and testing.
Each station is equipped with a radio frequency identification (RFID) reader, which collects data to optimize a manufacturing process. Items that are built also carry chips that hold data relevant to their production.
Fourth year B.Tech Automation Engineering Technology student, Amy Hasselman, worked with YuMi, a collaborative robot, inside the Learning Factory. She used the robot to assemble a handheld electric screwdriver from scratch. YuMi uses a vision system on its wrist to take pictures and assemble parts.
“Everything from my classes came together in one project,” says Hasselman “It’s no longer these separate entities you learn in class, write about it in a test and forget about. My project exposed me to the real projects happening in industry,”
“Before having a place like this, students who graduated would go into an environment where they needed to be mentored and where it took them a lot of time to get up to speed,” explains Tim Valters, chief executive officer, Surteco Americas Plastics Division. “A place like this is changing that dramatically. This is the future of manufacturing.”
Vince Guglielmo, vice president, Automotive Parts Manufacturers says that industry can improve their own practices by partnering with students in the Learning Factory.
“Industry can have direct input into the types of things students learn, practice and implement,” says Guglielmo.“They can then turn the projects into meaningful activities or initiatives in their own organizations.”