Long established university-industry cooperation
The Steel Research Centre was set up to formalize and expand McMaster University’s well-established research links to Canada’s steel industry. Now in its third decade, the Centre has strong industrial support and graduates from the Centre are providing technical leadership to the industry worldwide.
The SRC’s research program is designed by its member companies and addresses difficult problems in primary and secondary steelmaking, process optimization and control, hot rolling, advanced high strength steels and metallic coating technology. Whole-of-process mathematical models have been developed that combine principles of high temperature chemical thermodynamics and kinetics with data from extensive laboratory and plant trials. The research program is highly collaborative with industry and is strengthened by access to production facilities and the generous advice we receive from prominent steel metallurgists.
Structure
The Centre is structured to foster collaboration and communication. Formal project review meetings are held in late fall and early summer, where graduate candidates present their results and receive valuable feedback. As part of these meetings, the Centre’s Board reviews budget matters and approves future directions. Member companies’ interest in intellectual property is protected by a membership agreement which confers royalty free rights to use the research results.
Funding for research projects in the Centre comes from industrial membership fees, combined with research grants. Once a project proposal is approved by the Board, the Principal Investigator applies for grants under various programs of the Canadian federal government or the Province of Ontario. Since 2000, Centre projects have been awarded over $8M in operating funds and a further $15M towards capital costs to expand laboratory equipment capabilities. Individual member companies, then, benefit from a significant multiplier of about 9:1 on their annual contributions, as well as access to the Centre’s specialized test facilities.
We are grateful for the support of the following funding agencies:
Federal:
Natural Sciences & Engineering Research Council Programs
Collaborative Research and Development
Industrial Research Chair
Idea to Innovation
Strategic Grants
Alliance Grants
Canada Foundation for Innovation
Innovation Fund
Leaders Opportunity Fund
John R. Evans Leaders Fund
Provincial:
Ontario Centres of Excellence
Ontario Research & Development Challenge Fund
Ontario Innovation Trust
Ontario Research Fund
McMaster University supports Science-based Manufacturing as a key research area. The SRC combines research objectives established by the steel industry with government funding supporting wealth creation through science. Developing exploitable technologies motivates and sustains a talented academic research team for the benefit of the steel industry, while producing a stream of knowledgeable engineers ready to make careers in steel. There are three components to the SRC’s mission:
- Research leading to commercially relevant new approaches to ironmaking, steelmaking process control, waste processing, steel product design and metal forming technologies.
- Training of highly qualified personnel who can transfer new technology to the steel industry.
- Continuing education for steel industry engineers to enhance the receptor capacity for innovation.
Guidance from the Centre’s industrial members is an essential principle of the organization. We have built up a membership consisting of the world’s major steel producers, as well as suppliers and engineering consultants to the industry.
Centre membership
Membership in the McMaster Steel Research Centre is available to companies that have an interest in the steel industry as producers, suppliers or users.
Members pay annual membership fees and participate in decision-making and intellectual property as outlined below. The Members’ fees attract matching funds from Government agencies. Annual memberships, therefore, provide highly levered access to about one million dollars of research activity.
Membership commitments are for five years, with provision for withdrawal on six months’ notice. The membership agreement and intellectual property policy outline rights in, and measures to protect the value of, developments made by the Centre.
- Early access to research results.
- Pre-publication copies of papers.
- Semi-annual reviews.
- Access to short courses.
- Non-exclusive, non-transferable, royalty–free licences for in-house use of IP developed by the Centre’s research.
- Exclusive, transferable, royalty-bearing licence for IP developed by research contracts with the Centre.
- Research contracts use discounted OH rate (30%)
- Entitled to transferable, non-exclusive, royalty-bearing licences permitting commercial exploitation of IP to third parties
- Participates in Program Review Groups
- Board membership
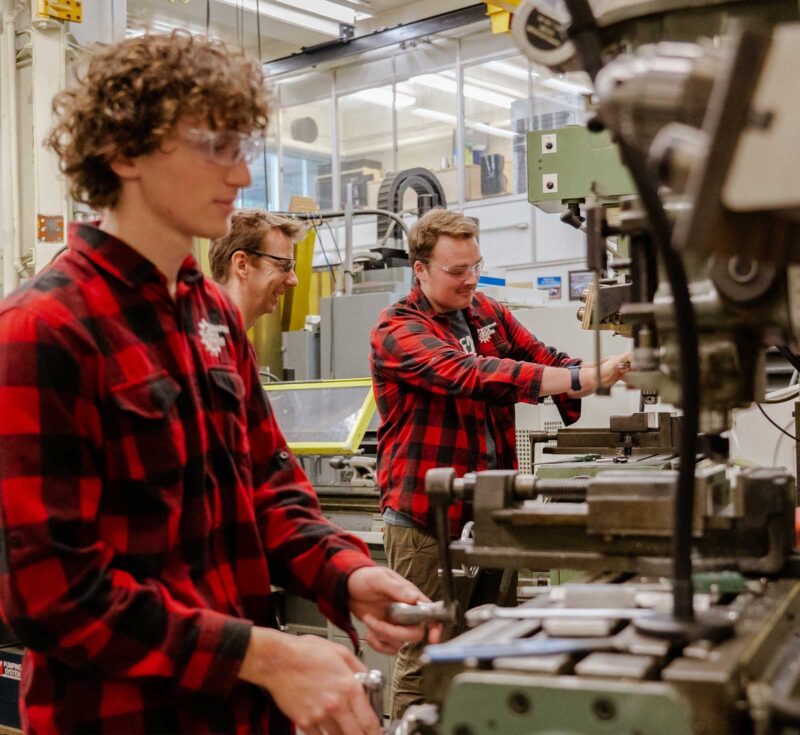
Contact us
Joe McDermid
Director, Steel Research Centre
McMaster University
JHE-343C
1280 Main Street West
Hamilton, ON, L8S 4L7, Canada
Tel: (905) 525-9140 ext. 27476
Fax: (905) 526-8404
John Thomson
Operations Manager, Steel Research Centre
McMaster University
JHE-211
1280 Main Street West
Hamilton, ON, L8S 4L7, Canada
Tel: (905) 525-9140 ext. 24955
Fax: (905) 526-8404