Powerful advancement
The Centre for Mechatronics and Hybrid Technologies is one of the most advanced research labs in the field of electrified powertrain testing, prognosis, and Fault Detection and Diagnosis (FDD) in Canada and internationally.
CMHT has state-of-the-art equipment obtained through multi-million dollar grants secured from the Canadian Foundation for Innovation, NSERC equipment grants, and Ontario Research Fund-Research Excellence (ORF-RE) awards
The ability to detect and diagnose faults is essential for the safe and reliable control of mechanical and electrical systems. In the presence of a fault, the system behaviour may become unpredictable, resulting in a loss of control which can cause unwanted downtime as well as damage to the system. There are two main types of methods to detect and diagnose faults: signal-based and model-based. Signal-based fault detection methods typically use thresholds to extract information from available measurements. This information is then used to determine if a fault is present. Model-based methods, as the name suggests, makes use of faults which can be modelled, typically through system identification. This type of fault detection and diagnosis is popular when well-defined models can be created and utilized. A number of fault detection and identification (FDI) methods are being implemented and developed by our research group. For example, one area of research involves developing a new neural network strategy to be used determining and predicting the presence of faults in engines. Another area of research involves the development of an interacting multiple-model approach, in an effort to correctly identify the presence of faults in an electrohydrostatic actuator (EHA).
Testing E-Axles, Electric Motors, Inverters:
- Efficiency Mapping
- Performance Characterization
- Fault Detection, Diagnosis and Prognosis
CMHT has state of the art facilities for testing the e-axles, motors and inverters used in electric and hybrid vehicles. This test equipment is used for advanced research in the areas of performance testing, test optimization, integration testing and with the advanced fault detection and prognostics software, we are able to provide unprecedented insight into e-mobility research.
CMHT is researching with major suppliers and users, battery cells, packs and battery management systems.
CMHT has unique testing capabilities with specialized testing equipment from Digatron and D&V Electronics. These resources allow CMHT to provide deep research into batteries, cells and the software running these systems.
Research areas include:
- EIS Model Fitting and Analysis
- State of Charge/ State of Health Estimation
- Li-Ion Battery Modelling
Case Studies:
Estimation theory plays an important role in a variety of fields – ranging from astronomy to commerce, and biochemistry to mechanics. It involves determining a value of some parameter of interest, typically by extraction from noisy observations. In engineering, one is usually concerned with the system states of a mechanical or electrical system. Quite often, the states are representative of the dynamics of the system. For example, one may be interested in the position, velocity, and acceleration of an actuator piston. Knowledge of these states is important for the successful control of the actuating device. The states are observed or measured by the use of sensors in the environment. However, measurements typically contain unwanted information such as system and measurement noise. It is the role of a filter to extract the useful information from the measurements, while minimizing the effects of noise and other unwanted disturbances. The smooth variable structure filter (SVSF) is a relatively new (2007) estimation strategy based on sliding mode theory, and has been shown to be robust to modeling uncertainties. It is a predictor-corrector method that makes use of an existence subspace and of a smoothing boundary layer to keep the estimates bounded within a region of the true state trajectory. This creates an inherently stable estimation process. This area of research involves advancing the development of the filter, and working on implementations (simulated and experimental) of the SVSF.
Automotive tracking systems are integral part of any autonomous driving system. A generic automotive tracking system performs several functions. The environment is perceived using sensors such as LiDAR, radar, vision sensor, ultrasonic sensor, and infrared camera. The acquired information is processed for detection and classification of objects of interest. Artificial intelligence and machine learning techniques are among pioneering approaches to tackle this issue. The noisy information about the objects are later employed to estimate the quantities of interest such as position, direction, velocity, acceleration, shape, size, etc. for each object. This information is essential for decision making process for autonomous driving functionalities. In CMHT we have developed our in-house car detection and tracking technology, which has led to a number of publications, and an experimental setup for on-road driving, data collection, and real-time detection and tracking. We aim to use information from different sensors and sensor fusion methods to extend the scope of the project.
Mechatronics is a multidisciplinary subject, involving mechanical, electrical, computer, control, and systems design engineering. In our research group, mechatronics engineering is used to unite the principles of mechanics, electronics, and computing to generate a simpler, more economical and reliable system. Recently, a novel electrohydrostatic actuator (EHA) prototype was created by combining a computer-controlled servomotor with a hydraulic actuator circuit. An EHA is an emerging type of actuator typically used in the aerospace industry, and are self-contained units comprised of their own pump, hydraulic circuit, and actuating cylinder. The main components of an EHA include a variable speed motor, an external gear pump, an accumulator, inner circuitry check valves, a double-rod double-acting cylinder, and a bi-directional pressure relief mechanism. The objective of the design was to provide an efficient and accurate method of actuating heavy loads. A variety of control strategies were studied and implemented on the system in an effort to enhance the system performance. For example, strategies such as fuzzy logic, PID, feedforward, and sliding mode control were implemented. The results of this research have led to a number of conference and journal publications.
Research facilities
CMHT’s research utilizes the state-of-the-art testing facilities located at McMaster Automotive Resource Centre (MARC). Specializing in collaborative research projects with automotive OEMs and Tier One’s, CMHT’s researchers work at CMHT and in our partners’ facilities.
AVL DynoTK 250 Dynamometer
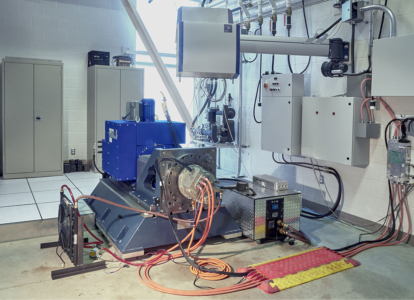
- 250kW Max Power
- 500Nm Max Torque
- 22,000 rpm Max Speed
- Maximum Acceleration 60,000 rpm/sec
AVL Puma Open Control System
- CAN communication up to 1000 Hz
- EMCON 400 Test rig controller
- Torque Measurement (up to 1kN, 0.05% accuracy)
- 16 high voltage analog inputs (1000V)
- 32 general purpose analog inputs (10V, 20mA, Thermocouple, RTD…)
AVL In-motion Simulation System
DC power up to 1000V, up to 800A
Various test inverters available to support custom E-motors
20kW fluid conditioning system
Horiba Dynas3 HT 250 Dynamometer
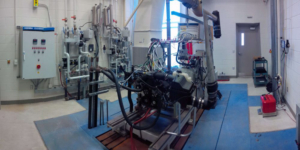
- 250kW Max Power
- 718 Nm Max Torque
- 10,000 rpm Max Speed
Horiba STARS Control System
- CAN communication up to 1000 Hz
- SPARCe Test rig controller
- Torque Measurement (up to 2kN, 0.05% accuracy)
- 32 general purpose analog inputs (10V, 20mA, Thermocouple, RTD…)
- 16 general purpose pressure inputs (various ranges)
Emissions Bench
Engine Coolant Temperature Conditioning System (200kW)
Engine Oil Temperature Conditioning System (40kW)
Miriam LFE intake airflow measurement system
Positive displacement volumetric fuel measurement system with on-line density meter
Mustang Dynamometer Chassis Dynamometer
- Duel 218 mm (8.575”) Roller
- Max speed 100 mph, 125mph transient
- Max 268 hp absorption
- 30” to 100” track width
- 6000 lb max axle weight
- 2000 lb mechanical inertia
Input Dynamometer
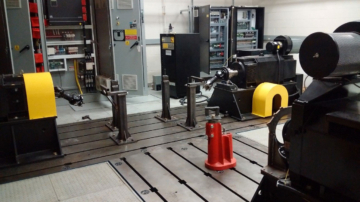
- Maximum Speed: 8000 RPM
- Maximum Torque: 1003 Nm (0 to 2000 RPM)
- Maximum Power: 210 kW (2000 to 8000 RPM)
- Overload capability
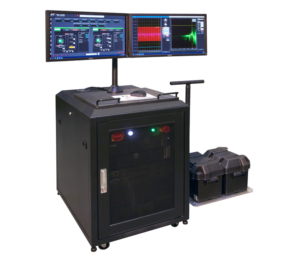
D&V BCT-150
- Full automatic switching between 3 test modules:
Cycler Module, High Frequency Signal Module and Coulombic Efficiency Module - 200KHz High Frequency Signal Module
- Expandable system, up to 16 Cycler Modules
Cycler:
- 1-6 V
- Current ranges: 5 A/25A/ 100A
- Expandable up to 16 100A Cycler Modules, allowing for testing one battery up to 1600 Amps or 16 batteries at
100A.
EIS:
- 1-6V
- Current: 5 A
- Electrochemical Impedance Spectroscopy testing (EIS) can be performed within a shorter period of time,
because we can automatically switch between the 3 test modules – 100 A Cycler Module, High Frequency Signal
Module and Coulombic Efficiency Module
Columbic:
- 1-6V
- Current ranges: 2 A/5A
- measurement reading up to 10ppm
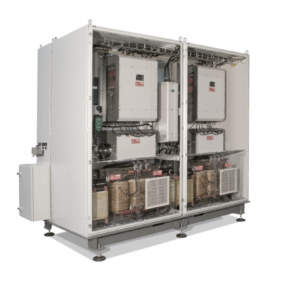
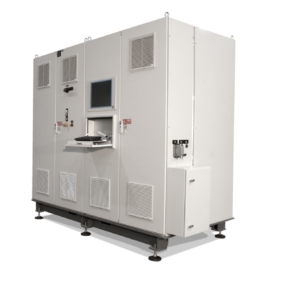
D&V Electronics BST 240 Battery Pack Tester
2 Independent Channels
- Max Current 400A/channel
- Max Voltage 600V/channel
- Max Power 120kW/channel
Two Channels in Parallel
- Max current 800A
- Max Voltage 600V
- Max Power 240kW
Two Channels in Series
- Max current 400A
- Max Voltage 1000V
- Max Power 240kW
HIgh speed switch mode – channel switching in ~100usec
- Max current 400A
- Max Voltage 600V
- Max Power 120kW
One 8 cubic feet Thermal Chamber -63 to +177°C
One 16 cubic feet Thermal Chamber -30 to 177°C
Thermotron SE3000 Environmental Chamber
- 3000l (100 cubic feet) capacity
- 70°C to +180°C (-94°F to +365°F)
Dual Servo-motor/pumps
Dual piston hydraulic cylinder with linear encoder
Simulation for leakage and friction faults
Dual Servo-motor/pumps
Dual piston hydraulic cylinder with linear encoder
Simulation for leakage and friction faults
Yokogawa WT1800 Power Meter
General purpose scopes, meters etc.
Vehicle hoist
Service Tools
Snap-on SOLUS ULTRA scan tool
dSPACE Micro Auto Box
Intrepid Controls NeoVI Fire/Vehicle Spy CAN Interface
Velodyne HDL32E Lidar
Delphi Electronically Scanning Radar
Princeton Applied Research Potentiostat/Galvanostat