The Centre for Automotive Materials and Corrosion works alongside leading scientists and industry partners on cutting-edge science to test the mechanical and environmental degradation limits of materials.
Focus areas
Third Generation Advanced High Strength Steels (3G AHSS) are capable of attaining high strength and ductility with appropriate heat treatment. Dr. McDermid’s group focuses on optimizing the composition and heat treatment parameters of these steels to produce an ideally strong and ductile material capable of being processed on a continuous hot-dip galvanizing line. Promising mechanical property results have ben obtained with 6 wt% Mn containing steels. Current work is on the mechanisms that form the microstructure during heat treatment and the effect of steel chemistry on the resulting microstructure.
Successful galvanizing requires contact between Zn in the bath and Fe in the steel. Careful control of the CGL atmosphere can promote reduction of native surface oxides or create internal oxidation exposing more bare Fe to the Zn bath. Dr. McDermid’s group works to understand the thermodynamic and kinetic parameters that control oxide reduction and internal versus external oxidation. As a result, the CGL can be operated in a more cost-effective and environmentally friendly manner.
A section of steel is dipped in the zinc bath for approximately 4 seconds during continuous hot dip galvanizing. During that four seconds, a chemical reaction called reactive wetting takes place between the steel’s iron and the bath’s zinc and aluminum. The intermetallic helps adhere the overlying zinc to the steel during further processing. By careful control of the atmosphere and holding times prior to dipping, the degree of reactive wetting can be varied, resulting in understanding of the kinetics of this process. This project is done by Dr. McDermid’s group using CAMC’s galvanizing simulator and meniscograph.
Steels require complex chemistries to attain their desired mechanical properties. Unfortunately, these complex chemistries can result in non-metallic inclusions (particles) in the steel that can collect hydrogen that would otherwise diffuse harmlessly through the steel. Collected hydrogen can eventually cause fracture of the steel, resulting in catastrophic failure of the part.
Dr. Kish’s group is working to understand which non-metallic inclusions in steel collect hydrogen and at what rate. Knowing the rate at which hydrogen collects allows an estimation of time to failure, while knowing which inclusions cause embrittlement allows development of alloys without those inclusions. This will improve lifespan and reduce the number of failures of critical infrastructure.
Undersea pipelines are coated to prevent corrosion. To assemble the pipelines, a section at the end of each section of pipe is left uncoated when leaving the factory. A coating is applied after welding at-sea to prevent corrosion around the welds. In some situations, the factory applied coating may debond from the pipeline, allowing Hydrogen to build up between the steel pipe and the coating. This hydrogen can then cause hydrogen embrittlement of the steel and unexpected rupture of the pipe. Dr. Kish’s group is investigating the risks of the debondment and the possibility that the at-sea applied coating affects the debondment rate.
Magnesium is a light, strong metal that suffers from severe corrosion in aqueous environments. Coated magnesium can suffer from filamentary corrosion, where thin corrosion bands travel along the metal/coating interface, resulting in disbondment of the coating and failure of the coated component. In this work, Dr. Kish’s group seeks to determine the parameters that control filament corrosion in an attempt to reduce the amount of filamentary corrosion on coated parts, thereby increasing their lifespan.
In this research, we work in partnership with a coating manufacturer to compare the corrosion protection provided by different coatings in various on two magnesium alloys of interest to the automotive industry. After panels were coated, the coatings were scribed through to the base metal, then exposed to salt spray conditions for 1000h. The corroded panels were then sectioned and examined to determine the type and extent of corrosion.
Future work will examine the electrochemical stability of the coatings to determine optimum processing parameters for corrosion prevention.
Applying a layer of corrosion resistant steel on a substrate of traditional steel improves the lifespan of the component and reduces the material cost. Understanding how these multi-layered steels perform in a variety of conditions will increase their applicability. Thermal cycling may affect the robustness of the layered structure, while the atmospheric corrosion rate may be highly susceptible to the dewpoint. This work, co-lead by Dr. Kish and Dr. Zurob seeks to determine the effect of high temperature and environmental dewpoint on the corrosion behavior of these steels.
The 7000 series of aluminum alloys are high-strength alloys under investigation for automotive applications. To attain the desired mechanical properties of the alloys, room temperature forming of these materials is not possible. Dr. Jain‘s project focuses on determining the forming parameters required to successfully apply AA7XXX alloys to the automotive industry. Formability is controlled by the dominant deformation mechanism at each potential forming temperature. Experimental work determines the deformation mechanism, with the results used to develop constitutive material models that allow our industry partners to evaluate the ability to form specific components from AA7XXX alloys.
To make automotive parts from sheet material, the maximum amount the sheet can be stretched and strain must be known. After determining the ideal CGL-compatible processing parameters for 3G AHSS, Dr. McDermid’s group determines the formability limits of the resulting sheet.
Third Generation Advanced High Strength Steels need to achieve high strength while maintaining acceptable levels of ductility, which make them promising for automotive applications. Understanding how these steels deform and break is critical to their application as it will promote alloy and heat treatment modifications to obtain optimal mechanical parameters. Using micro-DIC (microscopic digital image correlation), a technique pioneered by Dr. Wilkinson, his group has mapped deformation and its effect on the microstructure of 3D steels in both 2D and 3D. Results to date indicate that cracking initiates in blocky retained austenite, then moves into the ferrite with the final stage of cracking occurring in the martensitic phase. Coupling DIC with x-ray tomographic imaging of damage enables the development of robust models for fracture resistance and ductility enhancement.
This work by Dr. Wilkinson’s group uses X-ray tomography coupled with in-situ tensile testing to determine the mechanism that causes pure metals such as copper and magnesium to mechanically fail. The results show that damage is highly dependent materials class. While face-centred cubic metal such as copper exhibit isotropic damage that can be modelled using continuum mechanics approaches magnesium, which is hexagonal close packed develops microcracks that form on twin interfaces and grain boundaries then spread through the materials. As a result, the continuum-based damage models do not work for HCP materials that undergo deformation twinning. A new approach based on crystal plasticity approaches is needed to fully understand ductile fracture in these materials.
CAMC facilities
The CAMC features characterization, forming and corrosion labs and is equipped with a galvanizer simulator.
Our Iwatani-Surtec mimics the entire continuous galvanizing line with control over parameters including heating and cooling profiles, atmosphere and dew point, bath composition, dipping time, air knife type, angle, and flow rate, and the ability to quench. Samples can be heat treated without dipping to obtain optical alloy mechanical properties and understand fundamentals of microsctructure development and parameters that control the rates of internal and external oxidation.
Donated by Dofasco Inc. in 2004, the Galvanizing Lab also includes a meniscocraph which is used to asses the wetting of steel surfaces by molten metal.
CAMC has two Ascott Analytical salt spray chambers, one 400L volume, and the other 1000L volume. These chambers can run standard salt spray tests like ASTM B117 or SAE J2334, as well as custom cycles combining heating, cooling, humid, dry, and spray steps.
The chambers can hold samples like small coupons up to components up to 24″ in all three dimensions.
Chamber limits include temperatures up to 60C, salt, acidified spray, and controlled humidity between ambient and 100%.
Please contact Beth McNally for more information on this equipment.
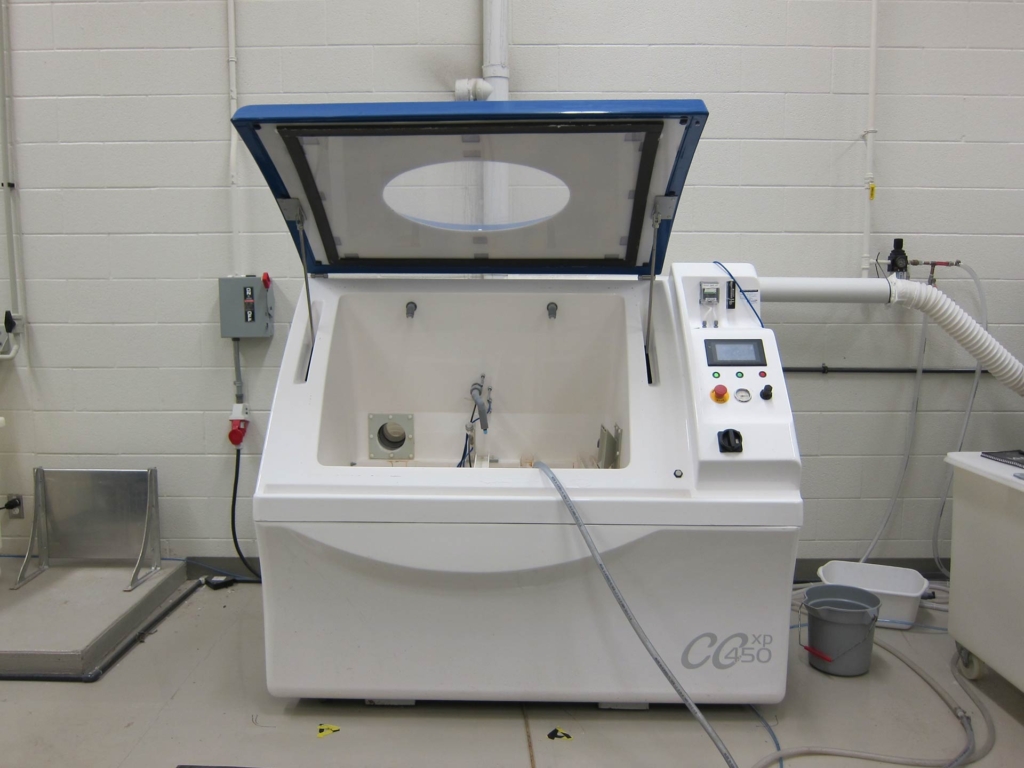
This equipment consists of a salt spray chamber built around horizontal a fatigue frame capable of both tensile and torsion loads The chamber can be programmed to run standard salt fog exposure tests as well as custom tests, both wet and dry.
The load cell capacity is 160 kN/1000 Nm with grips a minimum of 2″ and a maximum of 8″ apart. Current grips are clamping jaws for sheet up to 3.5mm thick. Minimum speed is 1mm/min, maximum is 1250 mm/min.
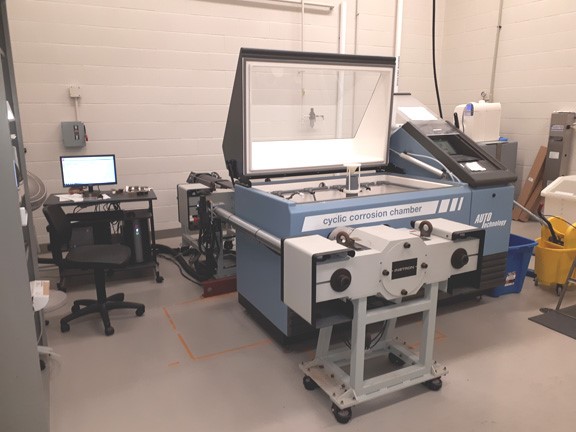
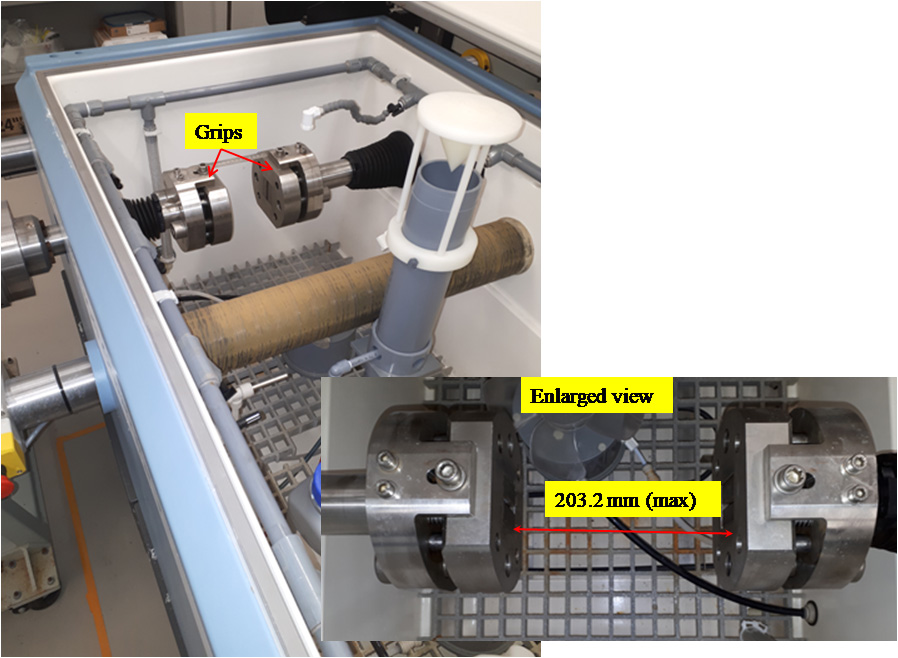
Potentiostats control and measure current and voltage. Changing either the current or voltage and measuring the system’s response helps to describe the corrosion suscepitbility and other properties of a material, coating, or assembly.
CAMC has seven potentiostats – 3 Gamry, 1 two channel Bio-logic, a Solatron, and an EG&G 273. All of the potentiostats besides the EG&G 273 are capable of impedance measurements. We use saturated calomel electrodes and have a variety of electrochemical cells and components to enable measurement of most configurations of samples.
Please contact Beth McNally for more information about our potentiostats.
CAMC is home to a Uniscan M370 Scanning Electrochemical Workstation. This apparatus performs spatially resolved electrochemical experiments, allowing us to determine areas on a sample that are reacting. The areas can be determined as a function of time, allowing the rate of reaction to be measured. The major techniques available on the workstation are:
- Localized Electrochemical Impedance Spectroscopy (LEIS)
- Scanning Kelvin Probe (SKP)
- Scanning Vibrating Electrode Technique (SVET)
Please contact Beth McNally for more information about the scanning electrochemical workstation.
The Walter Smeltzer Corrosion Laboratory at MARC has power supplies and other electrochemical equipment available and with standard laboratory glassware and equipment. We can develop apparatus and experiments to investigate corrosion and electrochemical phenomenon.
Please contact Beth McNelly for information about corrosion and electrochemical experiments available in the CAMC.
This 10 kN 5566 Instron tensile frame is suitable for testing materials with low moduli or thin films.
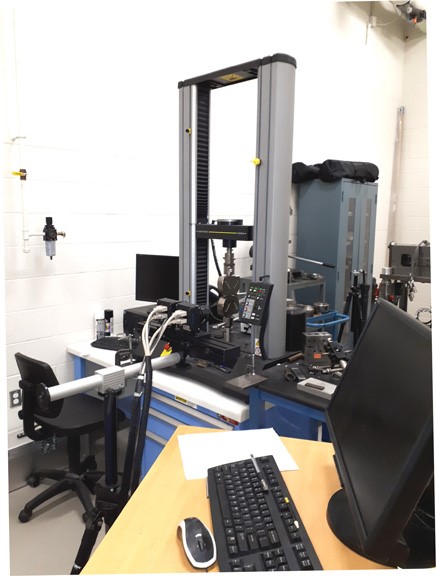
A four-column 100 kN MTS servohydraulic load frame equipped with two actuators.
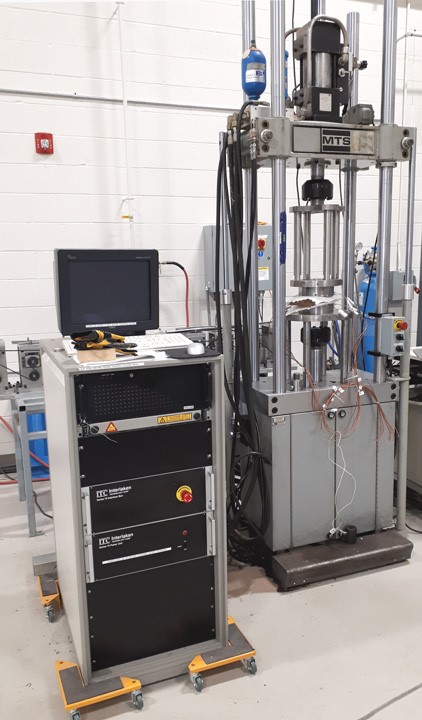
This two column 100 kN servo-hydraulic load frame is especially suited for fatigue experiments. It has hydraulic wedge grips for holding samples.
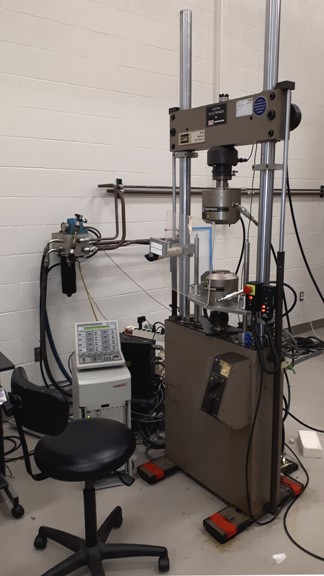
This two column 250 kN MTS servohydraulic load frame has hydraulic grips for holding samples.
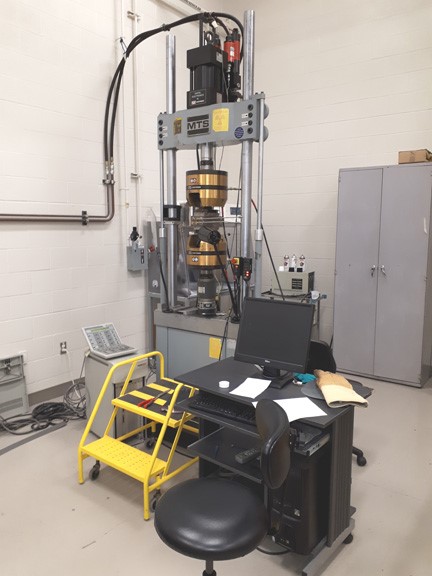
This two-column 250 kN MTS servohydraulic load frame is equipped with an environmental chamber capable of 5000 C maximum and -300 C minimum.
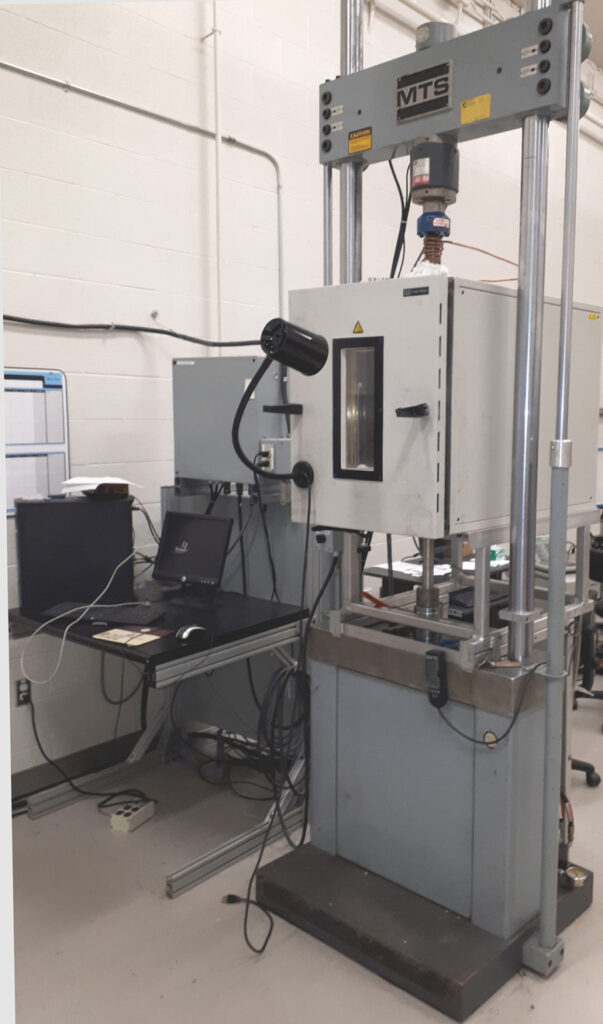
Digital Image Correlation is used to monitor deformation in realtime. Using high speed cameras, a series of images is taken as the sample is deformed. By comparing the relative locations of features on the sample, localized deformation data can be obtained. The Aramis systems used within CAMC use high speed cameras to obtain images, then processes them to obtain deformation data. For samples without surface features, a grid or random dot array can be applied to the surface to obtain data. The Aramis analysis software has also been used to characterize deformation in In-situ SEM images, as pioneered by Dr. Wilkinson and his group.
This lab has equipment and supplies to prepare samples for examination by microscopy, electrochemistry, galvanizing, or mechanical testing. The core of the laboratory is a precision cutter, hot mounting press, cold mounting equipment, manual grinder, automatic grinder, and etchants. The lab also contains large desiccators for sample storage.
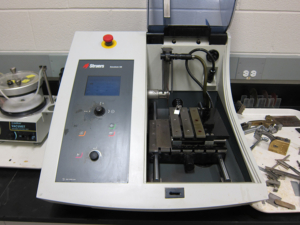
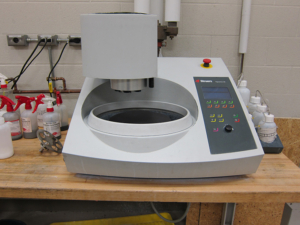
Capable of optical imaging up to 2000x, CAMC’s Keyence microscope is also capable of 3D imaging and stitching several images together.
Contact Beth McNelly for access.
CAMC is home to a SkyScan 1172 micro-computed x-ray tomographer suitable for the characterization of materials like metals, biomaterials, and composites.
CAMC is home to a magnetic saturation apparatus used to calculate the austenite fraction of steels.
CAMC houses a TA Instruments DLF 1200 Laser Flash Analyser used to measure thermal diffusivity, thermal conductivity, and specific heat capacity. Suitable samples are cylindrical either 12.7 or 25.4mm in diameter, up to 10 mm thick. The furnace is capable of heating samples to 1000C for property measurements at elevated temperatures. We also have a sample holder suitable for power or liquid samples.
A Linesys RITA L78 quenching dilatometer, capable of using inert atmospheres is part of CAMC.